This is going to be of little interest to anybody who doesn't have:-
(a) a car old enough to need a carburettor
(b) some DIY skills
(c) a degree of (not in) gung ho engineering.
My 1300 crossflow ex Ford escort engine had a twin-choke Webber carburettor, it is a fine design, but very complicated and, when old, fallible.
My answer was to try to fit a simpler device. Now I have always been fond of the SU carburettor. I had a chat with a man who has converted LandRovers to SU. He said it could be done and I arranged to have him make up a conversion pipe, basically a tube with sharp right angle bend. Sadly, before I could take the car to him to size the job up, the Webber threw a wobbler, no doubt sensing the end of a long career, and refused to leave the garage. I decided that I would have a go myself. Three main components are needed. An adaptor plate to go on the old Webber manifold, one for the SU input and a tube with a 90 degree bend to join them. The scrap in the picture is a number of metal plates from the heat exchanger that was in the old oil burning 'boiler'. I used the same stuff for the folding windscreen effort. Essentially 10th inch mild steel plate. I transcribed the shape of the two gaskets onto one and cut them out with an angle grinder, with 1.5 inch holes in the middle of each for the pipe to connect with. The hard work was cutting the holes in the middle, as they were too small for the grinder. The old standby of drilling small holes in a circle and then lots of filing, a good reason for not using thicker plates. Remember to leave a tab sticking out if you want to weld anything else on. I suggest you don't cut off any metal that isn't getting in the way until you are sure you don't want it. Little sticky-out bits are useful for attaching return springs and cable clamps. The mild steel bent pipe I found in a Metal work-shop, I believe specialist exhaust makers have the same sort of thing.
Stage two is a mockup of the mounting arrangements, to make sure nothing hits anything else when in operation, for instance mine is rotated through 45 degrees anti-clockwise from the usual SU position to avoid the air filter hitting the side panel of the engine bay and the float chamber resting on the rocker-box. Here (eyes right) I haven't cut out the round hole in the oblong plate, because I'm not sure yet where I want it. I would add two points here, one was that my SU float chamber is at a different angle (about 10 degrees) to the body, which means I wanted an angle of 80 rather than 90 between the adaptor plates. SU carbs quite often have an upward tilt of the air filter side, but the float chamber should be vertical. The second point is that you may need to thicken the gaskets, for good clearance, by 1/2 an inch. Having said that the arrangement should be able to operate more than 10 degrees from vertical, otherwise hills, bends and braking would stall the engine.
The picture below shows the device welded up, it warped a bit, but the gaskets and a little hammer therapy sorted that, and yes, it's a wooden spacer-gasket under the oblong plate, which can also be used to correct any unforseen tilts. The accelerator cable is held by the combination of part of a spitfire twin-carb assembly and a piece of metal that used to be the release key of an angle grinder. The only serious bit of adjustment was making a linkage rod out of a 6 inch nail, it needed a 30 degree twist to make it nice.
Side effects. I may have to run a water pipe around the adaptor angle, as the Venturi effect can cause frosting inside the pipe, an alternative is to funnel air from the radiator around it, thereby warming it. As yet it hasn't done any more than develop a 'dew'. The other problem is that occasionally the float chamber over fills. Engine vibration seems to cure it, so it's probably the Ford fuel pump being set to a higher pressure than the SU carb likes, and when it is ticking over the needle doesn't settle properly.
There are fewer carbs as simple and reliable as the SU, however there are a few variables apart from the size and tilt, ( this one's an HS4, 1.5") One is the needle in the middle, there are hundreds of different shapes, this one comes from a Wolseley 1300 and seems to suit. a 'Crypton tune' may indicate otherwise. the others are the piston spring and the one under the mixture adjustment. I'm not sure how important they are, but as before the Wolseley one seems to work for me. There are useful pictures and words on the SU site (sucarb.co.uk ) especially http://sucarb.co.uk/technical-h-type-carburetter-diagram
One side effect was that the SU tended to over-fill and leak, not a good thing, although better on a cross-flow as it doesn't drip on the exhaust manifold! The fault was that the Ford engine mounted fuel pump produced too high a pressure for the SU carb. About 6 psi rather than 1.5 psi. You can't open the pump and reduce the spring pressure, so the next best bet is an in-line reducer. I bought one from e-bay for £25 including postage and VAT or you can just search fuel pressure regulator
Since fitting the SU I have noticed a definite increase in power, although it is difficult to separate the causes, not least of which was some oil treatment, and of course I don't know how good the Webber should have been. Although I've just replaced the Solex on the Herald based Midge with a factory recon, I'm now quite tempted to do the same there. We'll see. There are lots of useful facts and diagrams on a website called http://www.sw-em.com/ especially http://www.sw-em.com/su_carbs.htm Much of it is about Volvos, but they have some similarities and the writer has an amusing touch. Good wet weather stuff, and nothing to do with the Swedish Embassy.


The SU stands for Skinner Union. The Skinner brothers being the inventors. They eventually sold up to W.R.Morris who in turn sold to Burlen Fuel Systems Limited of Salisbury who are still running. Who Mr Webber was, I have no idea, but I'm assuming he was German because the device is efficient, compact, and wildly over-complicated. When new. Unfortunately it is also beyond my understanding as it consists of a basic idea with modifications, intermittent bypasses, compensating valves, boosters, negative feedback loops and balancing devices. All well and good if the thing isn't worn out, or clogged in some obscure corner. Later I shall take some time to disassemble it and find out what it was supposed to do and what went wrong causing it to fail. Perhaps it's not so much over-complicated as old, and my brain isn't complicated enough.
Meantime, here's a picture or two of the new setup, It will require a bit more tuning, but I think I have sorted most of it. I should mention the company who found me the SU hs4 and reconditioned it. (£99 including postage and VAT). Unfortunately they seem to have folded since then. They did the same with the other (Triumph) Midge and located a rather obscure Solex B30PSE1 which is running very nicely.
The rotation gets the air filter out of the way of the side-panel of the engine bay, but not so far that it rests the float chamber on the rocker-box. I could have made it taller, but I don't want too much pipe between manifold and carb because it tends to ice up. It may need a wrap-around water pipe to warm it, but I'm trying to avoid that as it will start to complicate matters. The choke cable was an awkward fit, so I made a curved device from a large washer cut into thirds and welded together side by side, after chamfering the inside edges. That way the choke cable nestles in the slot and gives a longer travel. Two small bolts lock it to the plate (with the red dot second picture from the top) where the cable normally attaches. that accommodates the long travel required by the choke mechanism. I hope to find an inert material to make a better gasket between the adaptor pipe and the manifold. Wood seems to work for now! The air filter is cheap, cheerful, but above all small. Purists might say the float chamber is 5 degrees off the vertical as it doesn't seem to be on exactly the same axis as the carburettor, however I doubt that many of our roads are as level as that anyway.
Putting the fuel pressure reducer (adjustable) in line meant I could use the ford pump. That in turn meant I can turn the electric pump off, though it is useful for priming the system when it has been standing for a week or so.
Sorry this page is a bit of a guddle, I merged two of them and it resulted in some duplication, hopefully I have deleted most of it.
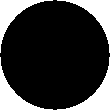
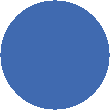


Choke cable
outer casing
carb body
Choke cable
inner wire
Pivot
Curved metal
thing made
from a 1.5"
dia washer